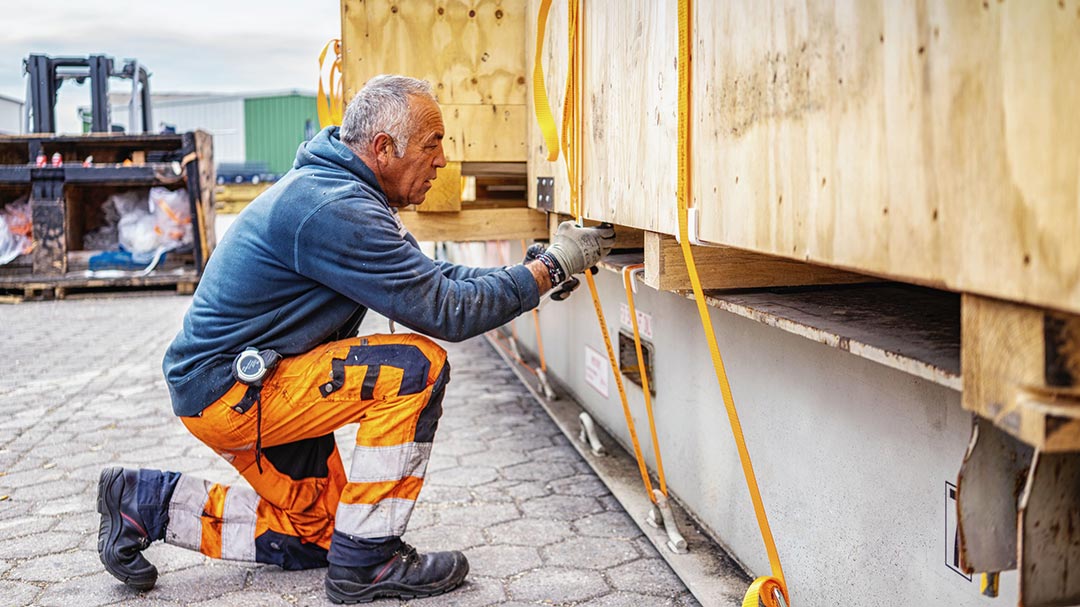
© offenblen.de/Marcus Barthel
For employees in the SACO-FCL project department, such dimensions – or larger – are all part of their everyday work. From breakbulk to project loading or roll-on/roll-off shipping – they organize the intake, marine transport and post-processing for these as well as standard containers. They know exactly what the maximum payload of this kind of specialized container is, with its solid base plate, and how wide, tall, and long the load – generally machines and equipment – can be per flat rack.
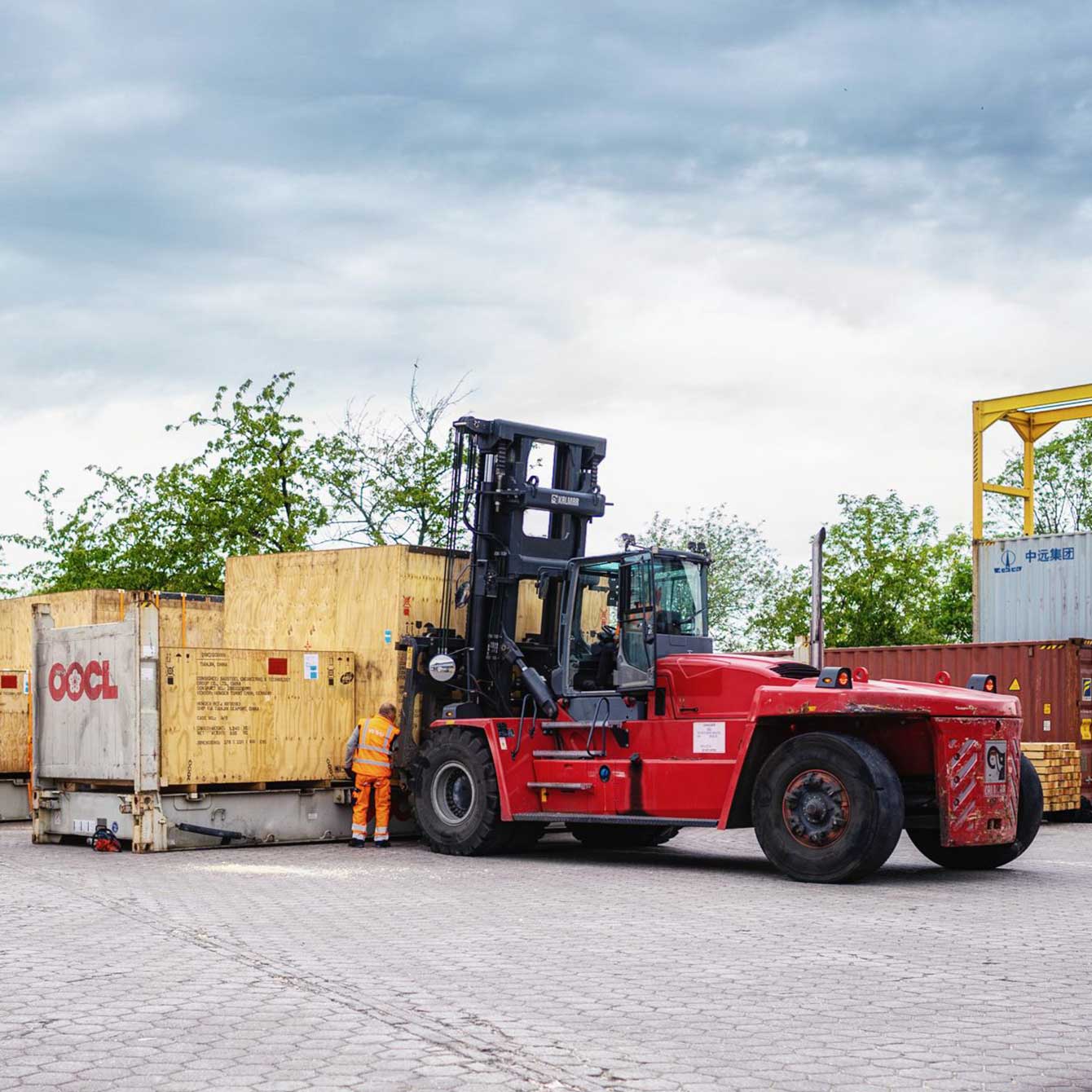
It should not be understated how much knowledge, experience and specialized equipment are required, and above all how much work is invested in conceptualization, consulting with customers, and coordination, so that ultimately everything can work together smoothly and reliably, and is conducted in a safe and timely fashion for both the load and employees.
As a storage and packaging company, WSG, which was founded in 1996 and integrated wholly into the SACO/PCH corporate group as a subsidiary in early 2018, specializes in packing containers. They handle anything that can be transported in or on a container, including specialized equipment. Two reach stackers are available for this work at the facility in Grasbrook, where the heavy-duty flooring has been compacted specifically for this purpose, each with a load-bearing capacity of 46 tons, along with four overhead cranes with a capacity between 10 and 30 tons. In addition, there are a total of 20 diesel and electric forklifts with a permitted load-bearing capacity between 3.5 and 33 tons, as well as over-height frames and specialized chains for transporting and handling 20- and 40-foot special equipment containers.
Since the SACO subsidiary moved to Schilfstraße in 2005 and expanded shortly thereafter to the neighboring property, a total of 30,000 square meters of space are available at the facility, including 8,500 square meters of warehouse and 1,000 square meters of roofed shed space. “This means we not only have more space for customers, but the added space also means extra safety for our 30 employees. And thanks to the hall roof, we can also protect large packages from the weather” explains Christian Brandt, authorized representative and General Manager at WSG.
Scoring points with customers through secure packaging and intake
Let’s get back to the two crates: “For safety reasons, we place them between the containers until they are loaded on the flat racks” explains Ivo Heitmann, Sales & Customer Service at SACO. Lots of materials are required on the flat rack as well to secure the load, like non-slip rubber and dunnage. “Sometimes, we also need to use support beams, such as if the crate wobbles when we lift it with the forklift”. If necessary, cross beams ensure the load is distributed evenly on the flat rack. “We also use squared timber, pressboard and rubber strips for lining under such crates” says Brandt.
Customers are aware that all these measures cost money: “They are prepared to pay to ensure the load arrives at its destination safely.” However, some things have changed. “There is an added challenge in a time when prices for wood are rising: People are saving on packaging materials and we have to be more careful during handling” Brandt reports.
While two of his colleagues lash the crates with orange straps, he explains: “Due to the movements of the ship during transport, we have to secure three times the weight.” Even though they don’t look like it, each strap can withstand up to six tons of hold-down force. It would be impossible to get the straps tight enough manually, so pneumatic strap tightening devices are used.
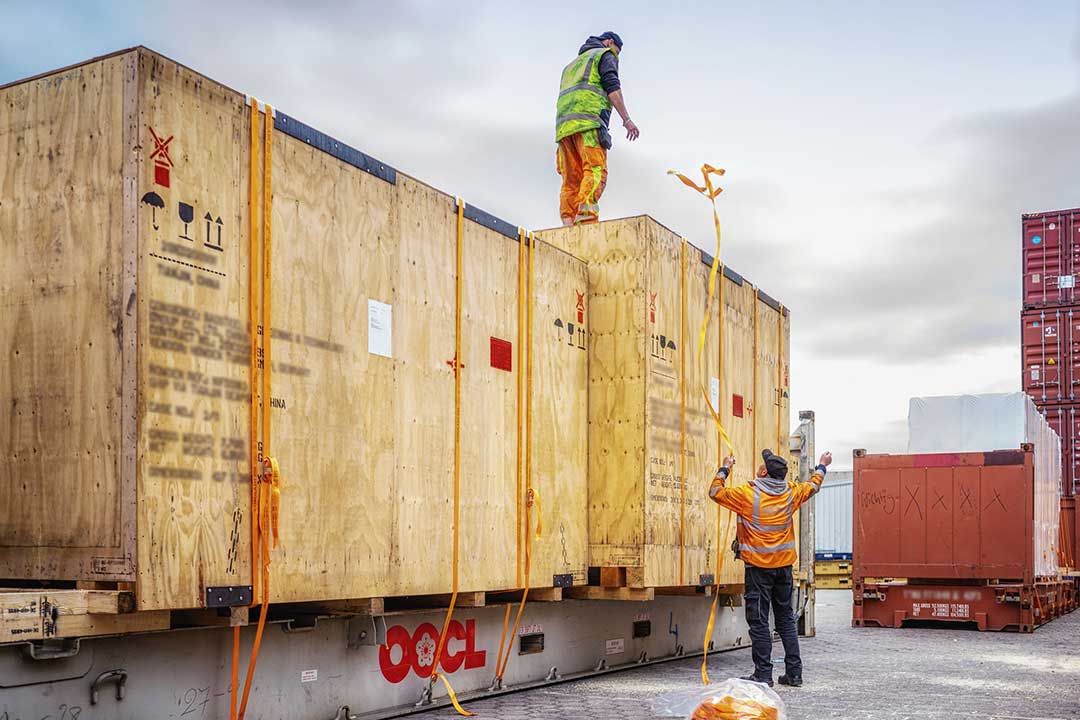
The biggest load: Rescue boats for the Bahamas
Unique selling point: everything from a single source
The unique thing about SACO is that it provides all services from a single source – from handling contact with the freight forwarder and subsidiary WSG, to truckers, haulage firms and shipping lines. The company’s good network is essential – to the packaging companies, subsidiary WSG, freight forwarders, and shipping lines. “Our customers really appreciate that we handle everything from A to Z, from inquiry to handling to documentation” Heitmann says. “There is also always one contact person per shipment order, supported by professionals in the different departments. In addition: “As a NVOCC, a non-vessel operating common carrier, we are always neutral towards our customers” underscores Andreas Fries, authorized representative and General Manager at SACO. “That means we work exclusively for freight forwarders.”
However, different kinds of challenges are all part of the job when handling bulky project, breakbulk, and roll-on/roll-off loads. “In large projects, it is important to think about and plan for every eventuality” Heitmann says. “Whether a crate is stackable, for example, is important, and whether a forklift can handle 30 tons during the overall transport” Wenzel adds. Ultimately, in the interest of the customer, it is important to ensure a crane isn’t required suddenly, resulting in additional costs.
Sometimes, collaborating with customers takes lots of flexibility: In general, clients provide packaging and the low-loader handles detailed coordination, for instance on individual dimensions, in some cases only shortly before pickup. “Because of this, we are available from morning to night, and if needed even by cell phone,” Heitmann underscores. Everything goes like clockwork for the two large, bulky crates. After all, there is nothing too large or too bulky for SACO.
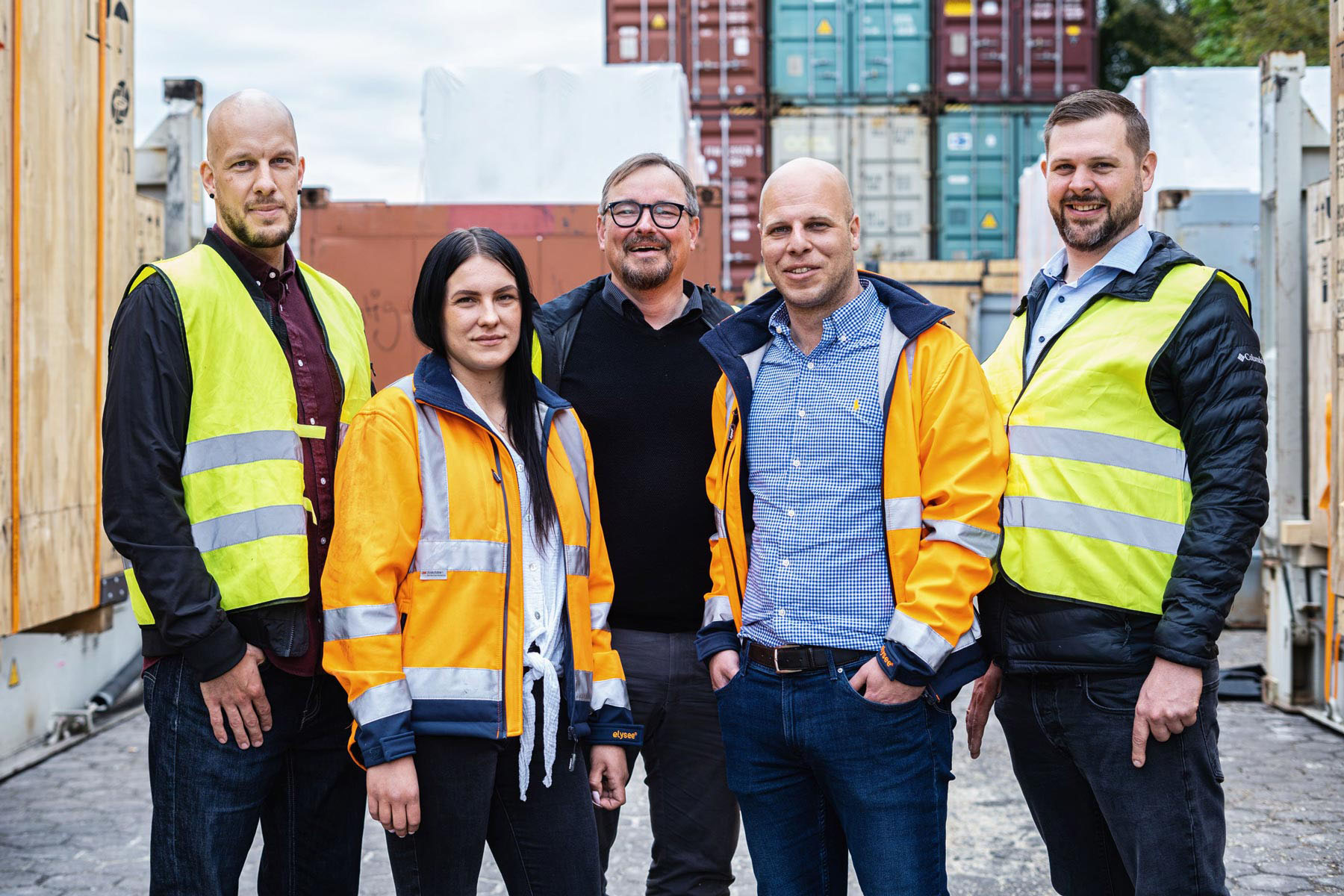
Ivo Heitmann, Sales & Customer Service at SACO
Jessika Ruschmeyer, Export und Disposition at WSG
Andreas Fries, Authorized representative and General Manager at SACO
Christian Brandt, Authorized representative and General Manager at WSG
Helge Wenzel, Sales & Customer Service at SACO
© offenblen.de/Marcus Barthel